石油・化学・食品・水処理などを担う「プラント」が、この事業の舞台。プラント設備工事の担当者として、徹底した設計・施工・工程管理のもと、安全と品質の両立を図っていきます。
岡本工業がこれまでに積み上げてきた経験と実績を生かし、安定した品質を確保しつつ、技術・技能を探求し続け、お客さま、そして社会に役立つ工事をおこなって下さい。

主な工事内容
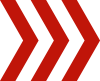
業務の流れ
- STEP/02
- 設計
-
基本設計
詳細設計
-
詳細設計
・各図面作成
・平面図
・立面図
・サポート図
・架台図
・スプール図
・製缶図
・3D-CAD図
・自社開発CAD図算
各計算
・配管強度計算
・構造物強度計算
・耐震計算
・圧損計算
・配管勾配計算
・熱応力解析
・配管肉厚算定計算
・圧力容器の構造計算
- STEP/03
- 施工準備
-
施工計画立案
材料手配
受入管理
-
各資料作成
・施工計画書
・施工要領書
・溶接施工記録
・工程表
配管材
・炭素鋼
・ステンレス
・塩化ビニル
・その他各種合金鋼
・各種継手、各種鋼材
- STEP/04
- 施工
-
配管内作
現場施工管理
検査・測定
引き渡し
-
製作工場
・千葉工場
・水島工場
・各常駐プラント内
内作場
管理
・安全
・品質
・工程
・コスト
精密機械部品などを製造する工場にて、お客様のニーズに合わせた設備保全工事をおこなっています。
工場の核となる工場内一括給水・給油設備のポンプ選定から設計、施工、引き渡し後のフォローなど、お客様の工場設備に関するさまざまなご要望に誠実にお応えし、お客様満足度120%を目指しています。

主な工事内容
工場一括設備工事
◆ 研削液循環一括設備の設計・施工
◆ 洗浄油循環一括設備の設計・施工
◆ 旋盤切粉処理一括設備の設計・施工
◆ 冷却水設備の設計・施工
工場施設の修繕工事
◆ 工場屋根の遮熱効果塗装工事
◆ 工場内壁塗装工事
◆ 工場床塗装工事
◆ シャッター、ドアノブなどの交換
◆ 駐車場の舗装工事
工場内設備工事
◆ 熱処理炉の補修工事
◆ 軸受研削機の移動・据付
◆ 搬送コンベアの修理
◆ 排気ダクトの製作・取付
◆ 危険物地下タンクの法的漏洩検査
◆ ホイスト設置工事
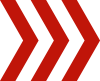
業務の流れ
- STEP/01
- 設計
-
基本設計
-
生産効率の向上、省エネなどお客様の要望にもとづいた現場寸法測定仕様書、P&ID、機器選定、機器配置計画、配管レイアウト計画作成
操作性、安全性、施工のしやすさ、メンテナンススペースを図面に反映
-
図面作成
各種計算
-
各種図面
・配管平面図、
配管立面図
・配管サポート図
・配管スプール図
・架台図
・機器(容器)製作図
など
各種計算
・圧力損失計算
・熱応力解析
・配管肉厚算定計算
・耐震計算
・鋼構造物強度計算
・容器強度計算
など
- STEP/02
- 施工準備
-
機器選定
-
目的、操作性、特性を考慮し、お客様の要望にあわせた選定
-
見積書提出
契約
機器調達
-
6軸自動盤を使い、自動車エンジン関連部品やベアリングなどを旋削加工しています。その数は、月産1,400万個にのぼり、多軸自動盤とNC加工機との組み合わせにより、複雑かつ高精度な製品の生産にも対応しています。
また、ISO9001に基づく品質管理はもちろん、社内生産設備の保守・保全、さらには使用刃具制作によるコスト低減などにも対応。ISO14001も取得しており、環境マニュアルに基づいたに省エネルギー・省資源活動も展開しています。

主な工事内容
品質保証
理念は、「一個の不良も流出させない」。生産現場での品質パトロールなどを通じ、日々の変化を見逃さず、万一の不具合に対してはスピーディーにフィードバックできる体制を確立しています。
また、月例の品質会議において製品の品質・変化点を各部署で確認し、品質に関する社内報を作成・回覧。徹底した情報共有で、品質の向上に努めています。
製造
「6軸自動盤58台」「NC加工機15台」を駆使した、月産1,400万個・24時間体制を誇る、信頼の生産体制が自慢。
製造現場では、稼働率の向上と不良率の低減を重要視し、無駄を省くことはもちろん従業員の教育にも力を入れています。
また、生産設備の保守・保全に関してはいずれも社内でおこなっており、安定した供給体制に責任を持って取り組んでいます。
生産技術
当社ならではの最適な工具の選定はもちろん、加工条件の設定にもこだわっています。また、鋼材の中でもステンレスなどの難削材を加工できる切削技術も兼ね備えており、その品質は折り紙付き。顧客の信頼も厚いです。
さらに、自社内で使用刃具の設計・製作をおこなっており、日々の生産をバックアップ。「1サイクル・1個生産」が通常の6軸自動盤において、当社は「1サイクル・2個生産」を可能とし、さらなる量産加工を実現しています。
近年はNC加工機を導入し、6軸自動盤で旋削したブランクに追加工または仕上げ加工を施し、6軸自動盤単体では難しい高精度・高付加価値を持つ製品を加工する技術を確立しています。
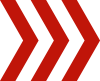
業務の流れ
- STEP/01
- 見積
-
工程検討
-
品質、納期を念頭に工程を検討し、お客様が満足できる見積もりを提出します。
-
材料調達検討
-
-
ツールレイアウト検討
-
見積提出と並行してツールレイアウト、刃具及び治工具の準備もおこないます。
-
治工具検討
-
- STEP/02
- 施策
-
試作品加工
-
試作品加工を通した評価・検証により、量産工程を構築します。
-
工程能力確認
-
-
ツールレイアウト検討
-
必要な帳票・標準類の準備をおこないます。
-
帳票・標準諸準備
-
- STEP/03
- 契約
-
契約
-
量産工程で初品を製作し、お客様の評定・合格判定後、契約となります。
搬送設備の検討・設計から製造設置までトータルで提案し、独自の搬送機器でお客様の抱える問題を解決します。
ここで設計・製造された搬送機器は、多種多様な工程で生産性の向上に貢献。コンベアやシリンダ、センサなどを組み合わせ、用途に応じた搬送装置を提供しています。

主な工事内容
設計
現場を熟知しているからこそできる設計を目指し、担当設計者がお客様との打合せ。お客様が抱える潜在的な要望をも反映させた設備を提案しています。
製造
40年以上にわたる搬送設備製造の歴史と、お客様の生産現場を支えてきた実績が裏付けする、高度な技術。
複雑な設計に対応する技術力に加え、急な設計変更にも迅速に対応できる体制のもと、長期にわたり安定して稼働する設備を製造しています。
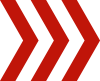
業務の流れ
- STEP/01
- 打ち合わせ
-
-
・条件の整理
・取り合いなどの確認
- STEP/02
- 構想
-
-
・コンセプトの確立
・構想図作成
- STEP/04
- 設計
-
-
・組図、部品図作成
・購入品選定